How is Cotton fibre converted into Yarn?
Let us first understand what is a cotton crop, from where it is originated and which countries and states in India are the biggest producers of cotton
Cotton is a Kharif crop, and its origin belongs to India from 3000 B.C. in the Indus River Valley (Present day – Pakistan). The cotton plant has been cultivated widely in over 90 countries for its fiber and seeds.
Cotton is an essential commercial crop cultivated in India and constitutes 25% of global cotton production. It plays a magnificent role in maintaining the livelihood of an estimated 6 million cotton farmers in India. Around 45 – 50% of the million people are occupied in related activities such as cotton production, processing, and trade. The other name for cotton is “White-Gold” due to its economic importance in India.
As of 2022, the top five countries in the world in cotton production are India, China, the USA, Brazil, and Pakistan. Nearly 22% of the world’s cotton production is produced in India, the third-largest exporter. India also stands 1st in the world in cotton acreage with around 120.70 Lakh Hectares area under cotton cultivation. India’s cotton is grown in two types of places – rain-fed areas and irrigated areas. The majority of the cotton production in India comes from 3 zones: The northern zone, the Central Zone, and the Southern zone, which includes ten states of India.
Northern Zone: Punjab, Rajasthan, and Haryana
Central Zone: Gujarat, Madhya Pradesh, and Maharashtra
Southern Zone: Telangana, Tamil Nādu, Andhra Pradesh, and Karnataka
Gujarat and Maharashtra are the top two leaders in producing cotton as the climate of both states is moist and well-suited for the cultivation of crops. Gujarat’s estimated cotton production for 2021-22 is around 92 lakh bales, and Maharashtra’s estimate is around 85 lakh bales released by the CAI (Cotton Association of India), according to the latest crop estimates. Bharuch, Panchmahal, Vadodara, Ahmedabad, Mehsana, and Surendemagar are the major cotton-producing cities in Gujarat.
Yarn Manufacturing
Now, after knowing the basics of the cotton crop and its producers, we will now tear into the manufacturing process of the same into yarn.
A series of processes in yarn manufacturing transforms unprocessed and raw cotton fibers into yarn that may be used in various end products. The clean, robust, and homogeneous threads needed for current textile markets require several techniques, which will be explained in detail below.
Cotton is a soft, fluffy, whitish-yellow flower that grows in a shell called a boll. The Cotton seed is sown in the spring from March-May, grown over summer, and plucked in autumn.
Before the 18th century, cotton fiber was processed traditionally by hand. The first automated processing machine was invented in the early 18th century in 1794 by American-born inventor Eli Whitney, who revolutionized cotton production by accelerating the removal of seeds from cotton fiber. Gradually, other processes were also invented.
Cotton Journey
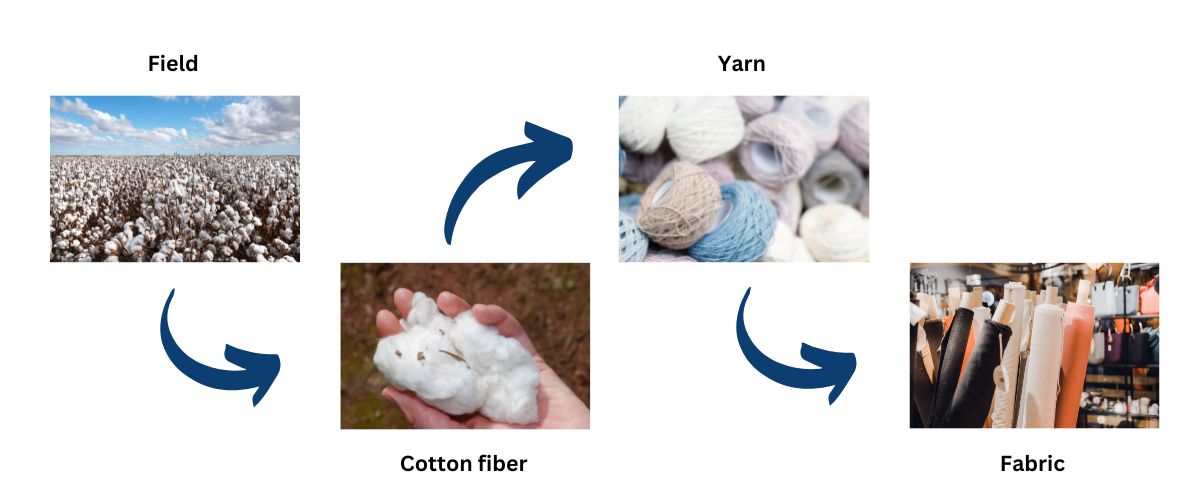
Cotton is generally used in the textile industry, and cotton fabric entails every type of clothing, from shirts to jackets to trousers. Cotton uses are also extensively seen in the Medical field, sanitary pads, diapers, bed sheets, and pillows. Here we will understand how unprocessed cotton is converted into yarn widely used in many end products.
Flow chart: From cotton field to final output of Yarn factory

Steps (Yarn Processing)
- Hand Plucked
- Ginning
- Spinning – Blow room, Carding, Draw frame, Comber, Speed frame/ Roving
- Ring Frame
Let’s dive into each stage.
Hand plucked
Cotton is a Kharif crop that requires almost eight months to cultivate. After sowing the seed into the soil takes 50-60 days for a flower to grow. The cotton is produced in a protective case called a boll around the seeds of the cotton plant. When the boll matures, it breaks, and we can find cotton popping out. This cotton is then harvested or hand-plucked and taken to the nearby gins.
Ginning
Gin is a facility or a type of plant where cotton ginning occurs. Ginning is the process of removing seeds and scrap from the cotton. In modern ginning, the cotton is first dried in dryers to reduce the moisture content and then is passed through a stage where they are cleaned thoroughly to remove unwanted foreign matters such as stems, seeds, debris, and leaves. The ginned cotton is called lint. This lint is converted into cotton blocks called bales and is sent to the spinning process.
(Note: The seed separated from the cotton fiber during ginning process is used in making cottonseed oil which is used in many household activities especially cooking.)
Spinning
Spinning is the process of producing yarn from the cotton extracted. Spinning involves many sub-processes, crucial in forming thread at the output.
1. Blow room
The bales from the ginning factory are brought to the blow room. These compressed bales of filers are opened and mixed. In this process of mixing, dirt, dust, seed particles, broken leaves, and foreign impurities are removed. This cleaned cotton fiber is converted into a sheet of definite width and uniform weight per unit length called lap, and the leftover cotton fiber is sent for recycling. This lap is rolled into a cylindrical shape around a lap pin and is sent to the carding process.
2. Carding
Carding is the second sub-process of the yarn manufacturing industry in conventional spinning lines. It is called the heart of spinning. The primary function of carding is to resolve any locks and clumps in the fiber received from the blow room. The fibers are made parallel and straight by opening and blending them through the machine, where short fibers are removed in the process, and the long cotton fibers are converted into a rope-like thread called Sliver, which is uniform in weight per unit length.
3. Draw frame
The Cotton Sliver obtained from the carding process is loose. It proceeds through a series of rollers to strengthen the loose assemblage of slivers, where each pair moves faster than the previous one. This process produces more uniform, straight, and parallel fragments by doubling the uneven short, medium, and long slivers.
4. Comber
The combing process removes the short fibers that are no longer needed, and long fibers are passed through a sequence of straight, metal teeth to make the fibers more parallel and serial. This process gives more clean and pure cotton fiber by removing dust, neps, and impurities which have settled during the operations. The primary function of the combing process is to produce clean, uniform, smoother, more refined, firmer, more parallel, neps-free cotton fiber for the following method.
5. Speed frame/ Roving
Speed frame is also called roving. Roving is a prolonged and narrow bundle of yarn. In this process slight twist is inserted to strengthen the roving and reduce it to the appropriate size. This low weighted twisted strand roving is then winded into a bobbin.
Ring frame
Ring Frame is the yarn manufacturing factory’s last and most important process. It gives the draft a roving until the required fineness is achieved. The objective of the ring frame is to add the necessary amount of twist to the fiber strand to keep the fibers in the yarn together and avoid slippage in the thread. This process simultaneously winds the yarn onto the cylindrical bobbin or tube while spinning and finally spin the required yarn count. At the end of the process, we get our final output called yarn.
Conclusion
The most universally grown and lucrative non-food crop worldwide is cotton. More than 250 million people receive income from its manufacturing, which also employs over 7% of all workers in developing nations. Cotton makes up roughly 50% of all textiles. For over 6,000 years, cotton has been farmed for food, fabric, and fuel. Cotton produces items like rope, paper, cooking oil, animal feed, packaging, biofuels, clothing, bedding, and towels. Humans cannot survive today without the use of cotton in day-to-day life. So quality product needs to be manufactured and for this purpose process of manufacturing unprocessed cotton into yarn involves many steps and process that requires proper and careful attention. It is fascinating to know how natural cotton can be converted into threads widely used in various end products.